Industry meets academia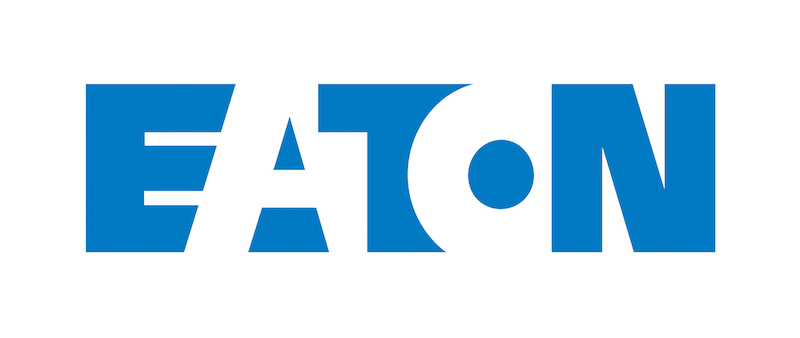
EATON Lab is a shared laboratory between Czech Technical University in Prague and EATON company. We join together to create a space that accelerates the flow of innovations from the university into industrial applications. EATON provides a feedback for students and academics to help them target research efforts to maximize the impact of their work. Most of the topics is suitable for thesis, so you can start gaining industrial experience already while studying. Work is flexible and takes into account that students need to finish their studies. If you are not convinced yet, you can read some student stories about what it is like to work for eaton and then check out our open projects and apply! :)
Open projects for students
Topic | Domain | Keywords | Level |
---|---|---|---|
Energy storage systems | Software | MATLAB, Simulink, COMSOL, thermal management system, battery energy storage systems, design, testing and validation | Masters |
SW platform development in aerospace domain |
Software, Embedded hardware |
MATLAB, Simulink, MBD, automation, testing, motor control, evaluation boards |
Bachelor+ |
Web UI for Electric Vehicle charger simulators |
Software | HTML, CSS | Bachelor+ |
Building testing infrastructure |
Software, Hardware |
embedded Linux, scripting |
Bachelor+ |
Python simulators for Electric Vehicle chargers |
Software | Python, EV, simulators | Bachelor+ |
Home automation systems |
Software |
IoT, Cloud systems, API, xComfort |
Bachelor+ |
Circuit breakers as HMI application |
Software |
C/C++, Python, Linux, industrials communication protocols |
Bachelor+ |
Visual Basic for Applications for Excel |
Software |
VBA, Excel |
Bachelor+ |
Student stories
"I started my master thesis during my internship at Eaton. The topic was about testing the endurance of the internal Flash memory of ASIC2. Later on to optimize the available areas of the Flash memory to be used as a virtual EEPROM for program variables. We designed a testbed PCB to test the endurance in different methods and then to test the optimized version. The final outcome of the project was an algorithm that allows the user to access Flash memory with simple functions as if it is an EEPROM." Ece A.
“As a student working in Eaton, I was working on creating an alternative emulated version of a SmartWire-DT module. For complete emulation I focused on both communication and performance characteristics of the existing SmartWire-DT modules and tried to implement them on some off-the-shelf components. I had to actively use many different aspects of the education I received in CTU such as Integrated System Structures, Microprocessors and Theory of Algorithms. The knowledge I obtained in CTU combined with the resources and help I received from everybody at Eaton made sure that I was able to complete my project and thesis successfully.” Tunahan Y.
"Jmenuji se Lukáš Doležel. Studuji na FELu navazaující magisterský program Elektronika a komunikace, obor Elektronika. Aktuálně u EATONu pracuji na projektu testování a měření baterií. Mým úkolem v rámci projektu je vymyslet program, který z naměřených dat z experimentů uložených v souborech vypočítá obvodové parametry pro náhradní obvodový model dané baterie. K práci používám MATLAB a vývojové studio pro jazyk C." Lukáš Doležal
Apply now
We provide competitive scholarships. In case you are interested in working on a project within the scope of EATON Lab, send an application letter to Adam Kollarčík (adam.kollarcik [at] cvut.cz).
If you have questions about topics or anything else, send an e-mail to Oxana Kovbasjukova (OxanaKovbasjukova [at] eaton.com).